Cleanroom lighting, often an overlooked aspect in design, plays a pivotal role in ensuring a contamination-free environment. Beyond merely meeting lux level requirements, it necessitates a thoughtful evaluation of its impact on airflow and filtration.
Here, we delve into eight critical considerations for choosing cleanroom lights, emphasizing the intricacies involved:
1. ISO Classification
The ISO classification of the cleanroom profoundly shapes lighting choices. Higher ISO classes prioritize ceiling space for filtration, presenting challenges for ISO class 5 cleanrooms. Practical options like LED batten lights with a linear shape become imperative, offering an appropriate footprint for surface mounting between HEPA or ULPA filters.
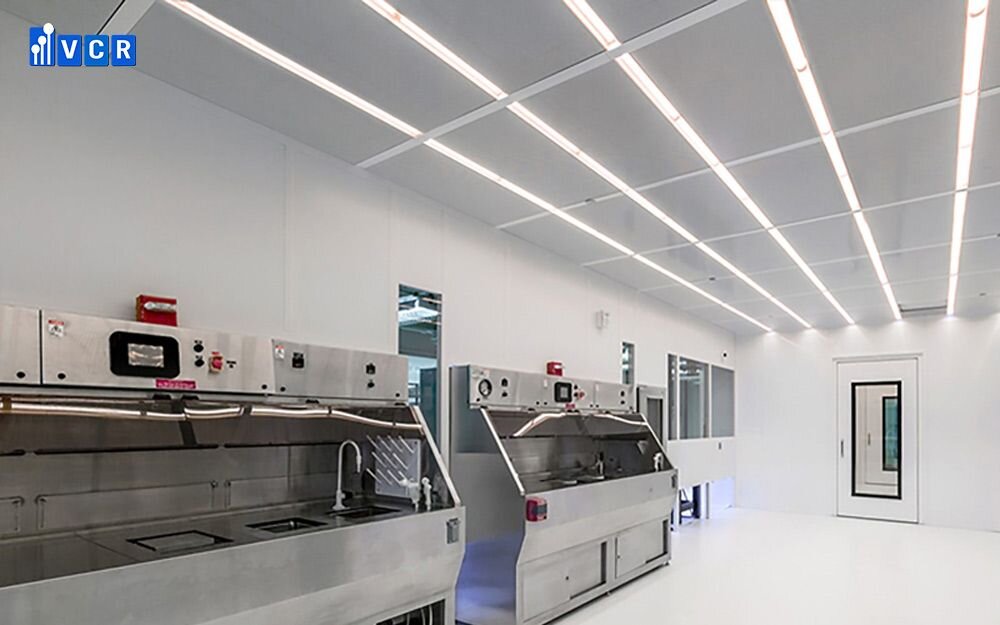
For lower ISO classes, where ceiling space is less restricted, flat-panel LED luminaires integrated into a monobloc ceiling with a flush finish present additional choices.
2. Service and Maintenance
Service and maintenance considerations are paramount during the cleanroom design phase. LED lights, surpassing fluorescent lighting in longevity and energy efficiency, are preferred. Roof-side replaceable lights, when feasible, facilitate external servicing without compromising cleanroom integrity.
Roomside replaceable lights, allowing replacement from within the cleanroom, prove advantageous when roof space is limited. If roof-side models are employed, ensuring walkability is essential for safety during maintenance.
Reference: Clean room light maintenance
3. CleanRoom Construction
Ensuring the facility meets lux level requirements involves utilizing lighting simulations during the design phase. Specialized light planning software facilitates the setting of a working plane and lighting output. Simulations allow for the assessment of even light coverage and identification of potential dead spots, preventing both over-specification and unnecessary maintenance.
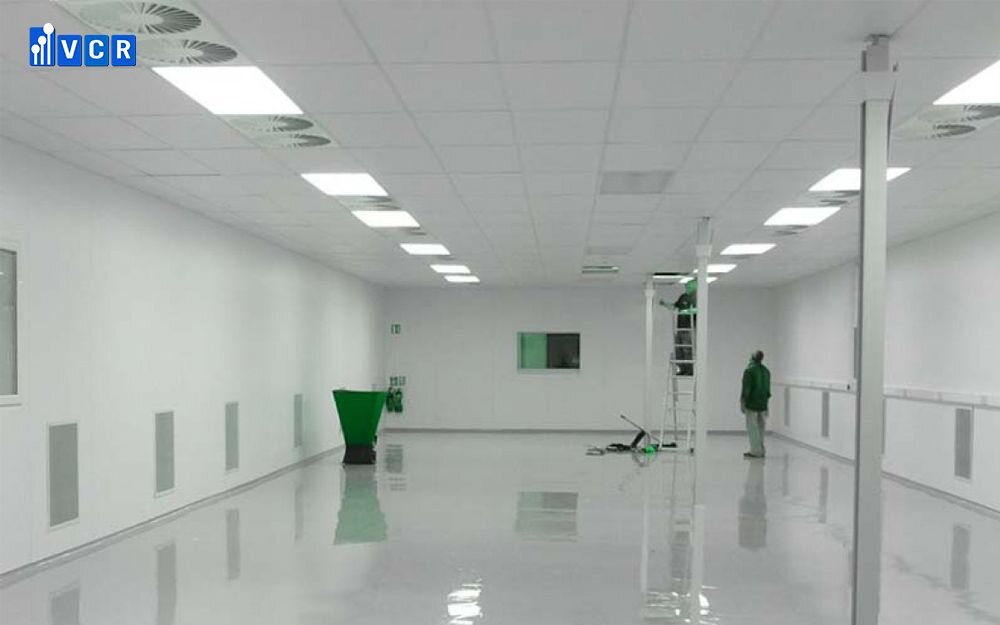
4. Lighting Control
Reflecting trends in home automation, lighting control features adaptive light levels for occupancy and customizable options. Designing lighting controls to meet individual requirements and budgets involves considering location, with pros and cons associated with manual control, cleanroom control systems, and automated control with passive infrared sensors (PIR) motion detectors.
5. Lux Requirements
Achieving the right lux levels is critical for safe and effective cleanroom operation. Driven by the production of small and sensitive components, minimum lux requirements vary based on tasks. Consulting the Chartered Institute of Building Services Engineers (CIBSE) Code for Interior Lighting provides recommended service illuminance ranges for various applications.
6. IP Rating
The Ingress Protection (IP) rating becomes crucial for controlled environments, signifying protection against solid objects and moisture. Choosing between IP45 and IP65 depends on specific cleanroom requirements and tasks, with careful risk assessment guiding the decision-making process.
7. Lighting Colour
Determined by Kelvin rating, lighting color temperature requires consideration based on tasks. Ranging from warm white to daylight, selecting cool white or daylight for task lighting is advised, avoiding over-specification to prevent visual fatigue. Coordinating lighting color with the cleanroom facility enhances continuity.
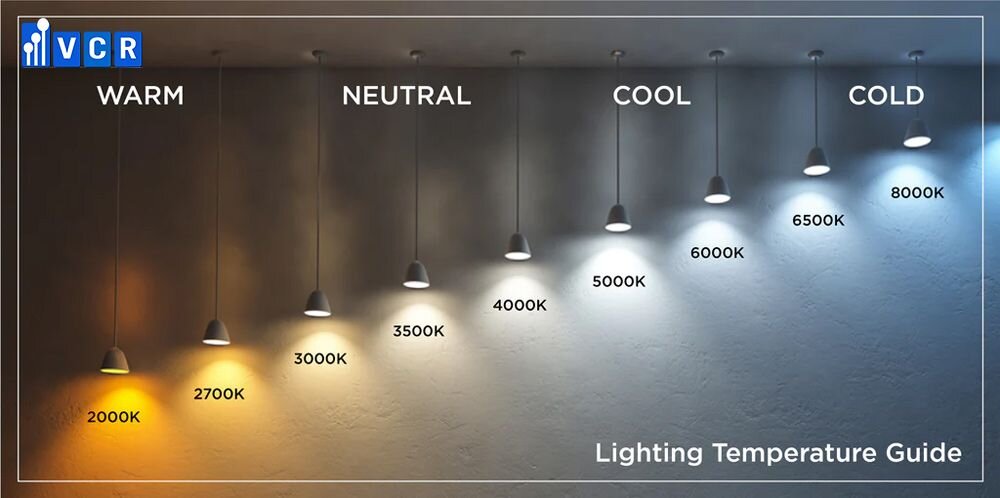
8. UV Lighting
While LED lighting serves general purposes, UV lighting finds niche applications in cleanrooms. Germicidal UV light supports disinfection without harsh chemicals, presenting budget and environmental benefits. However, considering health and safety implications is essential. UV torches aid training, while UV lamps prove effective for contamination detection in inspection work.
Navigating these considerations ensures a meticulous and informed approach to selecting cleanroom lights, aligning the lighting system with the specific needs and nuances of the controlled environment.
See more:
Clean Room Illumination: Strategies to Prevent Contamination